Water Damage Remediation at Construction Site
Background
We were contacted in August 2020 by a major property developer who had experienced water damage at one of their construction sites.
The building was undergoing major refurbishment works when a significant leak occurred on the 4th floor. It affected 26 flats, 8 communal corridors, the stairwell and reception.
We attended the site on the same day that we received the phone call, which was four days after the incident occured.
Obstacles and Challenges
We carried out a visual inspection, completed a thermal imaging survey and an in depth, non-invasive moisture survey.
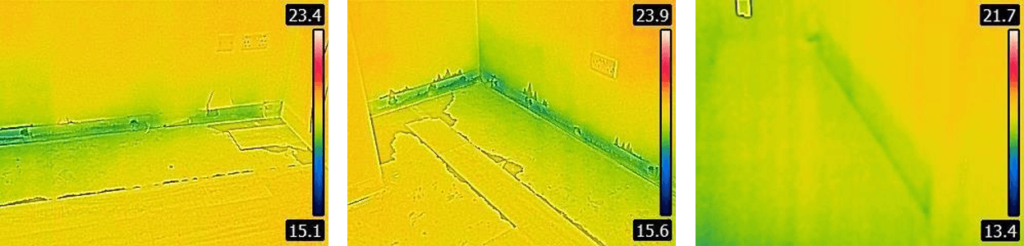
Due to the size and complexity of the situation we returned on two further dates to carry out a thorough investigation.
We were able to identify the moisture levels and damage throughout the building.
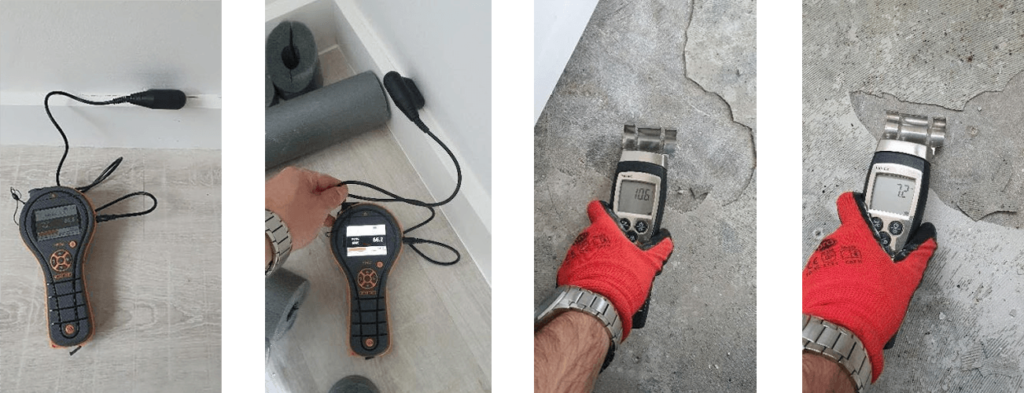
The damage was more extensive than originally thought, as most of the partition walls didn’t show any visible damage, however high moisture readings were recorded as the insulation within the walls had soaked up large volumes of water.
There was visible damage to lower walls, skirting boards, fitted units and floor coverings.
Large volumes of water had cascaded down the staircases, some of which was pouring out of the outer leaf of external walls.
Mould proliferation was already visible on the lower walls and skirting boards.
Time was of the essence as the flats were due to be handed over in two months time.
Our Solution
Following a visual site inspection, we gave site management verbal recommendations as to how to mitigate the damage.
After our full site inspection we put forward a report outlining the full extent of the damage, what was required to prevent further mould growth and an effective restoration proposal to remove excess moisture from the fabric of the building in a timely manner.
Our report contained two variants, as we were unable to identify if water had penetrated deep into the concrete floor and entered the cavity of the external walls. This would be determined by further investigations once strip out works had begun. The investigations would influence the drying methods used and drying times.
Floors
We recommended that existing moisture barriers be removed to facilitate drying the wet concrete floor. These included removing vinyl flooring, acoustic membranes and the self-levelling (latex) compound throughout all affected areas.
Due to the thickness of the bathroom tiles, we were unable to obtain accurate moisture readings of the floor. We suspected the floors had sustained damage, however we had been unable to confirm this. For this reason and to keep the cost of renovations to an absolute minimum, we recommended leaving the floor tiles in place and carrying our regular moisture readings in the bathroom.
Walls
Due to the insulation within the voids and its capability of absorbing significant amounts of water, we recommended a cost effective solution to strip one side of each of the affected partition walls and to remove wet insulation rather than to dry the walls with insulation in place. We therefore recommended skirting boards to be removed from all affected areas. One side of the plasterboard stud wall in the affected areas to be removed up to the electric socket level (approx 4400mm). Plasterboard to be removed from the walls at a high level (one side only) where required. Insulation to be removed from the exposed wall cavities. Plasterboard and insulation to be removed from the external wall up to 400mm height.
Ceilings
Where a significant amount of water had travelled through the ceiling, we recommended these sections of the ceiling and insulation above to be removed. Spotlights should be dropped down to allow air circulation in the remaining areas.
Drying proposal
We recommended the installation of three condensing dehumidifiers (Dri-Eaz 1200 or similar) and 6 air movers (Sahara E Turbo or equivalent) per plot.
Within 3 days of being appointed we delivered just over 10 tonnes of drying equipment to the site. Over the next 4 days a full drying regime was installed in all the affected areas, including drying of the external wall cavities full of water and wet insulation.
We had operatives onsite daily, taking moisture readings and signing off individual plots as dry, which meant the refurbishment could start quicker. The final areas were certified as dry three weeks after we began our drying programme, allowing the building to be handed over on time.